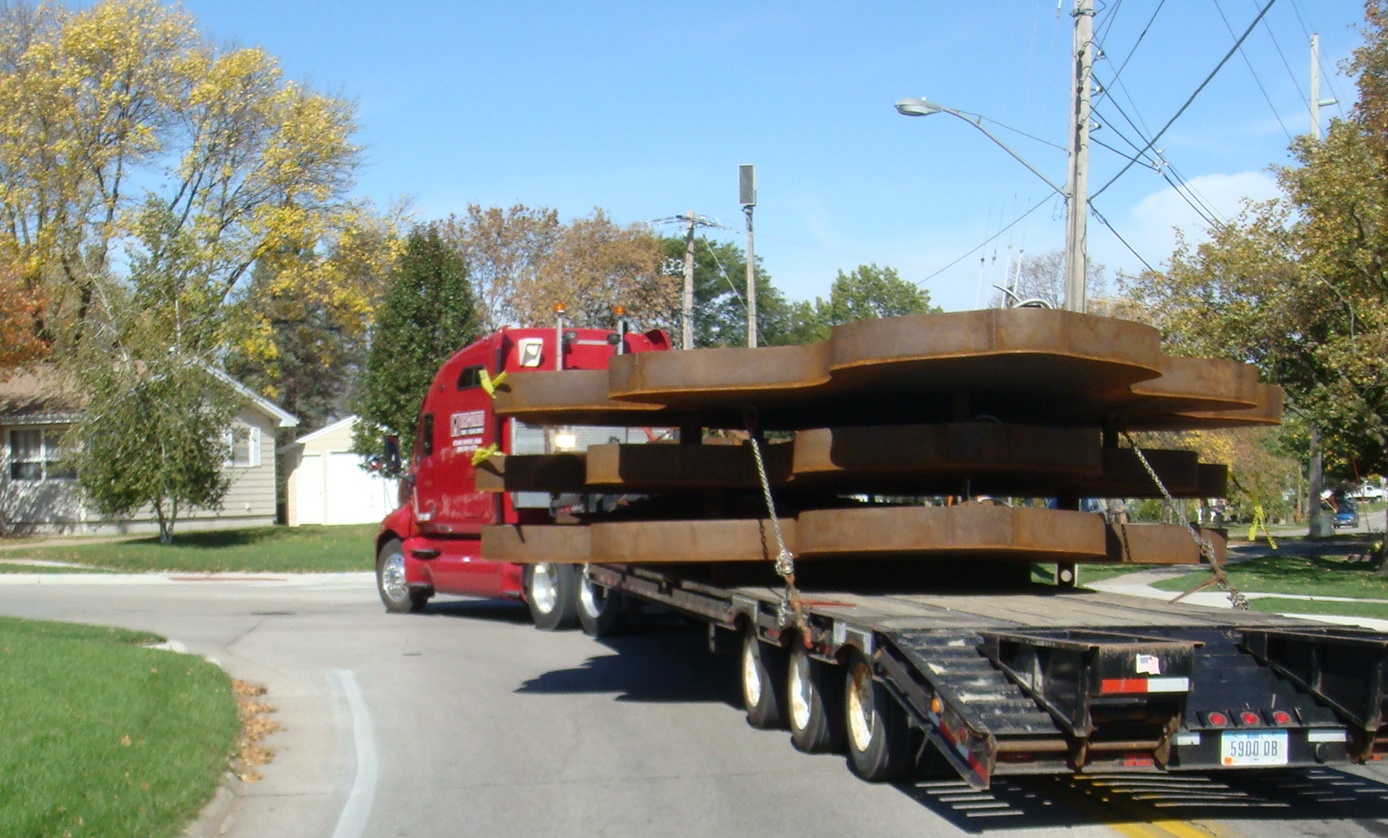
Determining the Feasibility of Your Innovation
Getting From Idea to Production
From napkin drawings to fully fleshed-out CAD drawings, Barnes has seen it all. Projects that often look great on paper sometimes call for ill-fitting or hard-to-source materials. Part of the Barnes process is a consult on the ‘build-ability’ of your project, and how much material sourcing is going to add to your budget.
Are Your Materials Feasible?
We have over 30 years’ materials expertise, and have seen both engineering and architectural plans that call for obscure materials or materials that don’t meet the physical requirements of the structure. Both of these issues can cause significant cost overruns that can be avoided with a materials consult. Having someone on your project team that can assist your architectural or engineering experts with material choices is a real advantage to meeting your bottom line.
Build-ability and Testing
Beyond material feasibility, product feasibility testing is part of the collaborative and iterative process of manufacturing. With small scale prototyping or mechanical testing, you can discover how your project will work off the page or even a 3D CAD drawing. More than requirements and constraints, knowing how buildable your project is can help you make decisions that impact budget before they send lines into the red.
Shipping Costs
At Barnes, we keep it tight. The machine shop is near the fab shop and paint shop. By keeping capabilities close, and not having to farm out wet coat paint or metalizing, our customers don’t have to pay exponential shipping costs. This can get extreme when you are talking tons. Make sure your custom manufacturing choice is clear about how far your job will travel before completion so you know what shipping to expect. Factors like proximity to rail, trucking and air freight hubs also are important to consider.
Want to learn more about custom manufacturing? Check out our case studies, project gallery, or contact us today.